In the competitive world of manufacturing and machining, the quality and durability of cutting tools are paramount. At Gandtrack, we understand that every detail matters when it comes to precision and performance. Our cutting tool coatings are designed to enhance your tool life, improve efficiency, and deliver the best results across a range of applications. Whether you’re machining aerospace components, automotive parts, or composites, choosing the right coating can make all the difference.
1. Titanium Nitride Coatings (TiN)
What It Does: TiN is a hard coating that enhances wear resistance and reduces friction. It provides a gold-coloured, smooth surface that improves tool life and cutting efficiency.
Applications: Commonly used on cutting tools like drills and end mills, TiN is effective for general machining of steel and aluminium. It’s not as suited for high-speed or abrasive materials.
2. Titanium Carbon Nitride (TiCN)
What It Does: TiCN combines titanium, carbon, and nitrogen to create a harder and more wear-resistant coating than TiN. It offers lower friction and higher toughness.
Applications: TiCN is effective for machining hard materials and composites. It’s used on tools for high-speed machining and applications requiring higher hardness and wear resistance.
3. Titanium Aluminium Nitride (TiAlN)
What It Does: TiAlN coating has excellent thermal stability and oxidation resistance, making it suitable for high-speed cutting. It provides a strong, hard surface and maintains performance at high temperatures.
Applications: Ideal for machining hard materials like stainless steel and high-temperature alloys. TiAlN is often used in aerospace and automotive industries for high-speed and heavy-duty applications.
4. Titanium Silicon Nitride (TiSiN)
What It Does: TiSiN combines titanium, silicon, and nitrogen to provide a coating with improved hardness and oxidation resistance. It also enhances thermal stability.
Applications: Used in cutting tools for machining difficult-to-cut materials and composites. TiSiN is beneficial for applications that involve high temperatures and abrasive materials.
5. Titanium Chromium Nitride (TiCrN)
What It Does: TiCrN offers a balance between hardness, wear resistance, and friction reduction. It provides better toughness and thermal stability compared to TiN.
Applications: Suited for general machining applications, including those involving tougher materials and composites. TiCrN coatings are often used in manufacturing tools and components that experience moderate to high wear.
6. Tetrahedral Amorphous Carbon (ta-C) (DLC)
This is the most commonly requested coating, and what we would recommend for most challenging applications.
What It Does: ta-C, a type of diamond-like carbon coating, provides exceptional hardness, low friction, and superior wear resistance. It has a diamond-like structure that enhances performance in extreme conditions.
Applications: Ideal for cutting tools used in machining hard materials and composites. ta-C coatings are used when maximum durability and a high-quality finish are required, such as in aerospace and high-precision industries.
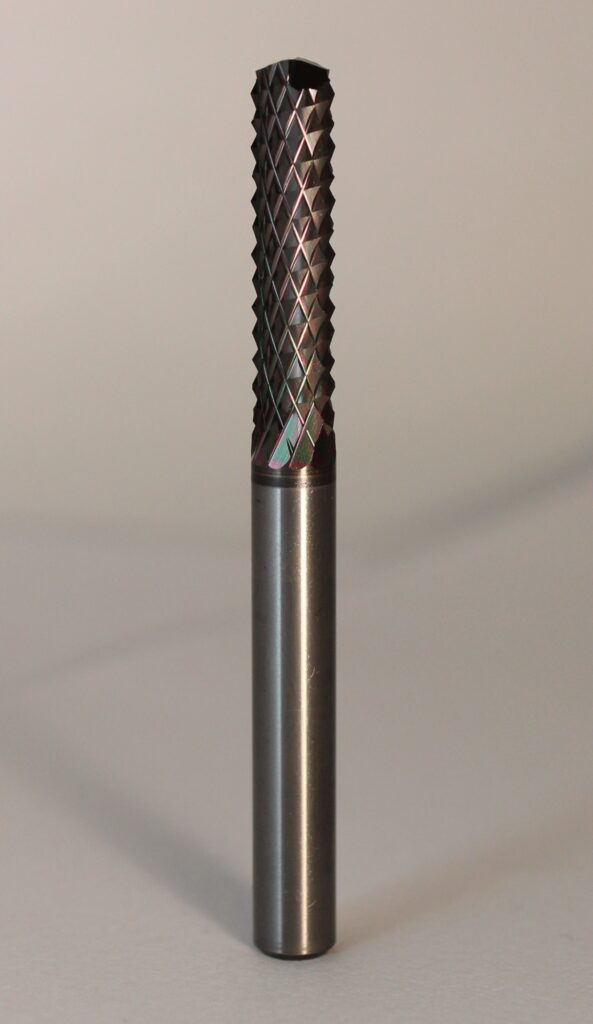
Comparison in Applications
- TiN: Best for general applications where moderate hardness and wear resistance are needed. Not suitable for very high-speed or abrasive operations.
- TiCN: Offers higher hardness and wear resistance compared to TiN, making it better for machining harder materials and composites.
- TiAlN: Provides excellent performance at high temperatures and speeds, making it ideal for tough materials and high-precision applications.
- TiSiN: Enhances both hardness and thermal stability, suitable for high-temperature applications and abrasive materials.
- TiCrN: Balances hardness and toughness, useful for a wide range of materials, including tougher composites.
- ta-C (DLC): Superior in hardness and wear resistance, ideal for high-performance cutting tools used in demanding applications with composites and hard materials.
Choosing the right coating for your cutting tools can significantly impact your machining efficiency and product quality. At Gandtrack, our commitment to innovation and excellence ensures that our coatings not only meet but exceed industry standards. By incorporating advanced coatings into your operations, you’re investing in tools that deliver exceptional performance and durability.
Discover how Gandtrack’s cutting-edge coatings can transform your manufacturing processes. Contact us today to learn more about our range of tool coatings and find the perfect solution for your needs.