Precision drilling matters. In the world of aerospace and composite applications, precision is not just a desirable trait – it’s an absolute necessity. From aircraft components to spacecraft structures, the integrity and reliability of materials used are of utmost importance. One crucial aspect often overlooked is the process of countersinking, a seemingly mundane step that holds significant importance in achieving the desired level of precision. In this blog, we’ll delve into the critical role of precision drilling countersinking in aerospace and composite applications and introduce the innovative solution: micro-stop countersink cages.
The Significance of Precision Drilling and Countersinking
Countersinking is the process of creating a conical recess around a hole’s rim. This seemingly simple procedure is paramount in aerospace and composite applications for several reasons:
Structural Integrity
In aerospace, components need to fit seamlessly together to maintain the structural integrity of the aircraft. Countersinking ensures that fasteners, like screws or rivets, sit flush with the material’s surface, preventing any protrusions that might cause aerodynamic disturbances or weaken the material.
Weight Reduction
Composite materials, often used in aerospace due to their high strength-to-weight ratio, require careful handling to prevent delamination or damage during the assembly process. Precision countersinking ensures that fasteners do not cause undue stress points, maintaining the material’s integrity and reducing unnecessary weight.
Aesthetic Appeal
In addition to functional considerations, aerospace components often need to look polished and professional. Precision countersinking contributes to the aesthetics of the finished product, making it visually appealing while maintaining functional excellence.
Introducing Micro-Stop Countersink Cages
Micro-stop countersink cages are revolutionary tools designed to address the challenges of achieving precise countersinks in aerospace and composite applications. These tools offer a range of benefits that contribute to accurate hole preparation:
Depth Control
Achieving the right depth for a countersink is critical for fastener installation and component assembly. Micro-stop countersink cages provide precise depth control, ensuring that every countersink is consistent and accurate. This eliminates the risk of over-drilling or under-drilling, which could compromise the material’s integrity.
Uniform Countersink Angles
Aerospace components often demand specific countersink angles to accommodate various fastener types. Micro-stop countersink cages are engineered to maintain uniform countersink angles, which is vital for fastener alignment and load distribution. This consistency minimizes stress concentrations and maximizes the component’s structural efficiency.
Improved Consistency
Hand-operated countersinking tools can introduce variations due to operator technique and fatigue. Micro-stop countersink cages eliminate this variability by providing a stable and controlled environment for the countersinking process. This consistency translates to enhanced overall quality and reduces the risk of assembly errors.
Precision DRILLING AND Countersinking
In conclusion, precision countersinking is not a step to be underestimated in aerospace and composite applications. It directly influences structural integrity, weight reduction, and overall aesthetics. The introduction of micro-stop countersink cages has revolutionized the way precision countersinking is achieved, offering accurate depth control, uniform countersink angles, and improved consistency. As the aerospace industry continues to push the boundaries of technology, these tools are instrumental in maintaining the high standards demanded by modern aircraft and spacecraft, to find out more about the countersink cages that we make here at Gandtrack, take a look here.
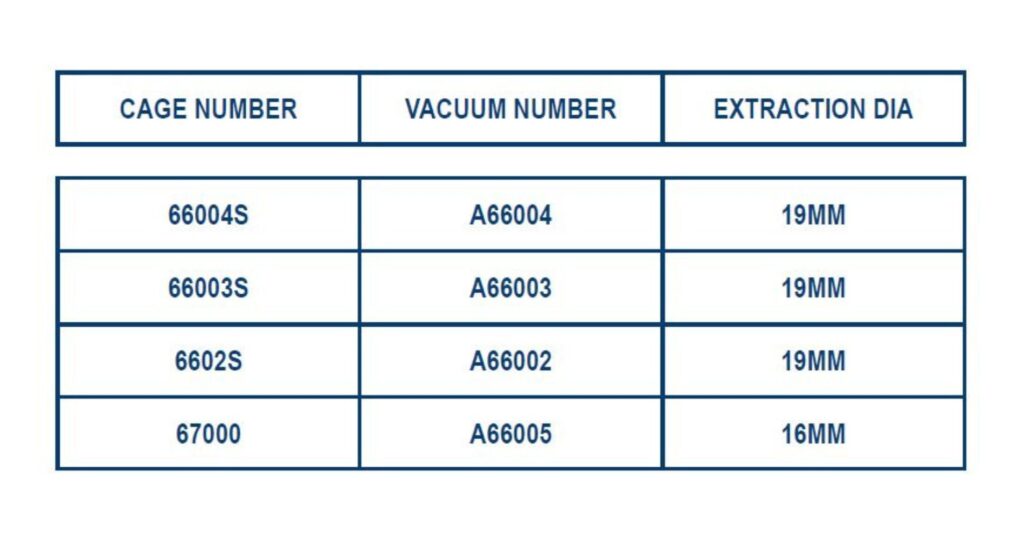
Why Gandtrack for Countersinking
Gandtrack have been supplying countersinks and countersink cages for decades. Specialists in cutting tools for the aerospace industry amongst others, we supply high quality tooling for composite cutting applications. We will support your exact requirements specification with tools that are fit for purpose and delivered at speed.
Based in Oldham, Lancashire, our team can also provide you with our technical support and advice to help you get the most out of your tooling. Speak to us about our smart tooling options, known to make efficiencies in cost and time. Call our team on 0161 627 2627 or contact us.