When choosing the right cutting tools for composite materials, it is important to understand the properties of both the tool and the material. This blog explains a number of drill types and applications.
Although composite materials might seem like a modern invention, they have been around for thousands of years. Wattle and daub, a mixture of mud and straw was used by the Egyptians because the straw added integrity to their mud bricks.
Fast-forward to the 20th Century and the use of composite materials in manufacturing became more commonplace, with the arrival of fibre-glass in 1935.
In a short time, composite materials have become an integral part of modern manufacturing due to their exceptional strength-to-weight ratio and versatility. From wind-turbine blades to carbon-fibre car bodywork, composite materials allow for the production of robust parts, without compromising on weight.
However, working with composites can be challenging although they can look and feel like metals, they act very differently while being machined. Metals are good conductors of heat, which makes drilling them relatively easy. In comparison, a composite insulates heat. That means the material is highly abrasive, which creates wear on the tools, reducing the life span of the drill bits being used.
Using the wrong cutting tools for composite materials can also damage the composite. That’s because composites consist of bonded layers of fibres and resin. When a drill bit pushes through these layers, it can cause delamination – the separation of layers. Delamination weakens the material’s overall strength. To prevent this, careful drilling techniques and specialised tools are essential. This ensures that the material’s layered structure remains intact, preserving its mechanical integrity.
That’s why choosing the right cutting tool is so important. Here we’re going to explore various cutting tools for composite materials, discussing the advantages and considerations associated with each type.
Dagger Drills
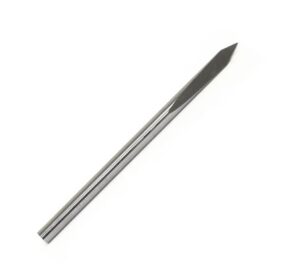
Solid Carbide Dagger Drills are specialised cutting tools for composite materials with dagger-like tips. These drills are engineered for precision drilling across a range of materials, including metals like stainless steel and titanium, as well as other composite materials.
Advantages of using dagger drills include:
Exceptional Hardness: This ensures extended tool life.
Precision: Solid Carbide dagger drills will provide outstanding and accuracy during drilling.
Geometry: Reduced drilling forces and heat generation reduces the risk of material damage.
Chip Evacuation: Enhanced chip evacuation for improved hole quality due to reduced risk of material damage.
Surface Finish: Suitable for applications demanding high levels of accuracy and a superior surface finish.
Considerations when choosing solid carbide dagger drills include:
Set-up: The need for a stable and rigid drilling setup will be required fully utilise their capabilities.
Cost: Solid Carbide dagger drills may be more expensive than standard drill bits. A cost-effectiveness evaluation should be conducted based on specific drilling requirements.
Carbide Brazed Tipped Tooling
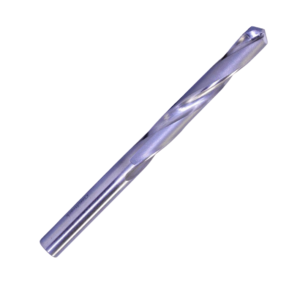
Carbide brazed tipped drills are well-suited for a wide range of composite materials. They offer a balance between durability and precision.
Advantages of using carbide brazed tipped cutting tools for composite materials:
Durability: Carbide-tipped tools can withstand the abrasive nature of composites and provide a longer tool life compared to traditional tooling materials.
High-Speed Machining: These tools can handle higher cutting speeds, resulting in improved productivity.
Cost-Efficiency: While more expensive than traditional tooling, carbide-tipped tools offer an excellent balance between cost and performance.
Considerations when using carbide brazed tipped tools:
Material Compatibility: Ensure that the carbide grade used in the tooling is suitable for the specific composite material you’re working with.
Coolant Usage: Adequate coolant usage is essential to prevent overheating and prolong tool life.
PCD Tooling (Polycrystalline Diamond)
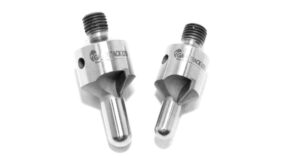
PCD tooling is an ideal choice when working with highly abrasive composite materials. The diamond cutting edges provide exceptional hardness and wear resistance.
Advantages of using PCD tooling include:
Superior Wear Resistance: PCD tools can handle highly abrasive composites, maintaining sharpness and tool life over an extended period.
High-Speed Machining: PCD tools can withstand high cutting speeds, enhancing overall efficiency.
Surface Finish: PCD tooling often produces a high-quality surface finish, reducing the need for additional finishing steps.
Considerations when using PCD tooling:
Initial Cost: PCD tooling tends to have a higher initial cost due to the use of diamond materials.
Fragility: PCD cutting edges can be brittle and susceptible to chipping if not used correctly.
Solid Carbide Drilling Tools
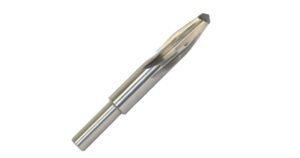
Solid carbide drilling tools are designed for precision drilling in composite materials. They offer accuracy and reliability for hole-making operations.
The advantages of using solid carbide drilling tools include:
Precision: Solid carbide drills provide accurate hole diameters and positioning, critical for assembly and component integrity.
Chip Evacuation: These tools often feature specialised flute designs for efficient chip evacuation, reducing the risk of workpiece damage.
Minimal Delamination: Properly designed solid carbide drills can minimise the delamination and fraying of composite layers.
Considerations when using solid carbide drilling tools:
Feed Rates: Optimising feed rates is crucial to prevent overheating and premature tool wear.
Drill Design: Select a drill design that suits the specific composite structure and thickness to avoid issues like tear-out.
As we’ve already discovered, care is required when machining composites. Their stacked-laminate construction makes them susceptible to delamination and damage to the fibres, particularly if cutting tools are worn or dull. Any fibre damage will immediately impact the strength and reliability of the composite.
Choosing the right cutting tools is essential to ensure the efficiency, precision, and longevity of both the tools and the finished products.
Consider the type of composite material you’re working with, the required level of precision, and the overall manufacturing goals when selecting between adapter drills. By making informed choices, manufacturers can achieve optimal results in their composite applications.